我们先认识一下IATF16949,在维基百科上的介绍是
IATF 16949原来名称为ISO/TS 16949,是国际标准化组织(ISO)的技术规范,目的是发展品质系统,可以在车辆供应链以及车厂中进行持续改善的系统,着重在预防缺陷、减少变异及浪费。此标准是以ISO 9000标准为基础,第一版是在1999年6月发行,名称为ISO/TS 16949:1999。此标准是由国际汽车工作组(IATF)以及ISO的“技术委员会”所订。主要在调和各国品质管理系统的规定。
因为车用产品有人身安全的考量,对产品的可靠度要求较一般电子产品更高;因此,只要是车用产品供应链的一环,都需要有IATF16949的认证才可卖产品给客户。
那么五大核心工具又是什么呢?这五大核心工具分别是
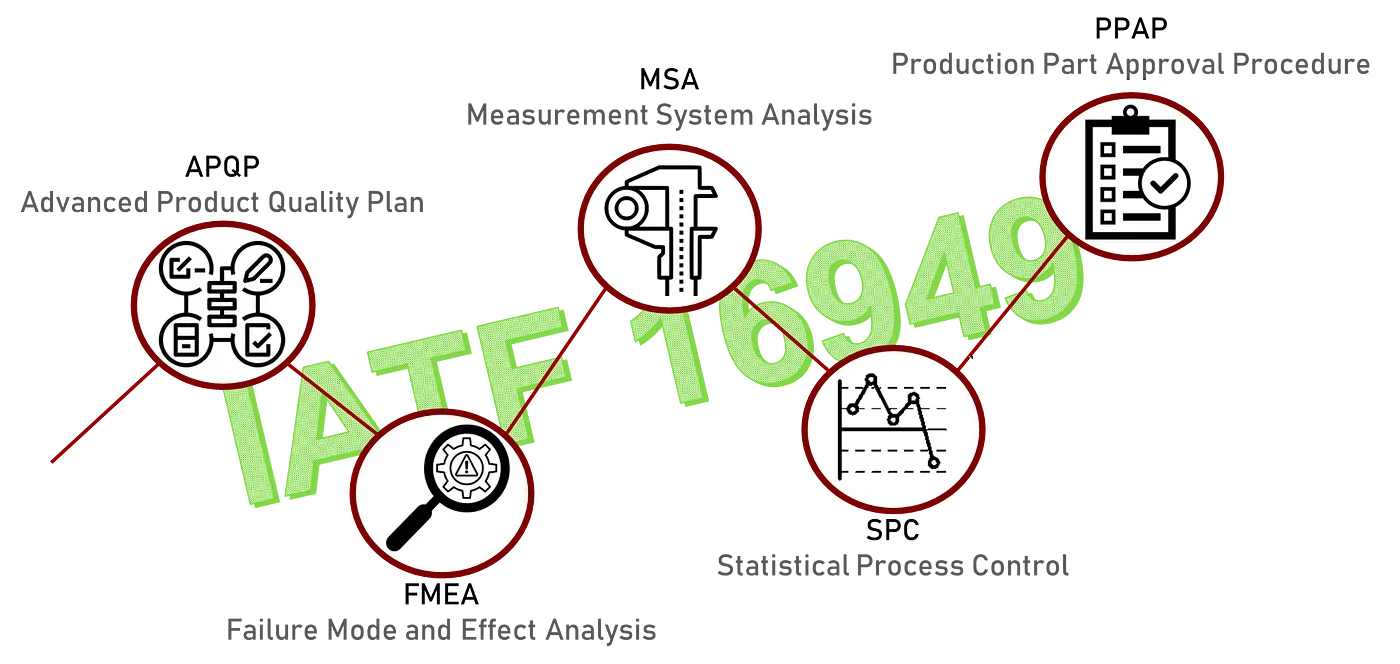
APQP(Advanced Product Quality Planning)先期产品品质规划
FMEA(Failure Mode and Effect Analysis)失效模式效应分析
MSA(Measurement System Analysis)量测系统分析
SPC(Statistical Process Control)统计制程管制
PPAP(Production Part Approval Process)生产件批准程序
这五大工具的目的在于透过系统化的方式,提早发现产品设计、制程设计、生产等各方面的潜在问题,从而确保产品品质可以满足或超越客户期待。
以下针对五大核心工具分别介绍
APQP
新产品开发到交付全部过程的策划、执行与控制,一般产品开发流程步骤包含
● 规划
● 产品设计开发
● 制程设计开发
● 产品与制程验证
● 量产
在APQP的各阶段中可兼容使用其他工具,确保整个开发流程的品质,详细内容可参考之前写过的新产品开发流程管理的工具APQP
FMEA
主要应用在产品设计与制程设计阶段,也就是APQP的二、三阶段所进行的失效模式分析,常见的有DFMEA及PFMEA,亦即产品尚未正式量产前,针对构成产品的子系统、零件及过程中的每一步骤进行分析,找出所有可能的风险,并依据评价结果采取预防性的措施。
● DFMEA: 在展开新产品、服务或流程设计前,先进行分析以了解展开后可能会产生哪些失效状况。找出会导致安全疑虑、功能错误、产品生命缩短、或顾客满意度降低等的问题。
● PFMEA: 用来改善既有的制造流程,以了解人员、物料、设备、方法及环境等如何造成制程问题。找出有哪些制程问题会导致安全疑虑、产品或服务缺失或降低制造良率。
旧版的FMEA使用RPN(Risk Priority Number)来针对严重性(Severity)/发生性(Occurrence)/检出性(Detection)进行评分,针对RPN高的失效模式优先改善
2019年AIAG&VDA合作整并各自的FMEA,新版的FMEA改采AP(Action Priority)进行改善,针对行动优先级高(High)、中(Medium)、低(Low)采取降低风险需求的措施,采用七步法进行解析
MSA
MSA是以简单的实验设计和统计分析方法,以数据统计与图表分析来评估测量系统的能力、性能和有关所测量值的不确定性。主要目标是量化测量系统的有效性,分析数据的变化并确定其发生变异的可能来源。
除了16949中定义的量具需进行评估外,下列情况也须进行MSA:
● 购买新的量具
● 客户要求或制程要求时
● 每当引入新的或不同类型的测量系统时
● 进行任何制程改进措施之后
● 对当前的测量系统进行了任何的改进
● 量具校正时
为了获得正确的测量数据,需区分出制程变异与量测变异,依据数值型态可使用不同分析
● 连续型: Gauge R&R (Repeatability & Reproducibility)
● 离散型: Kappa analysis
SPC
SPC是一种利用统计方法进行制程管制的工具。它对生产制程进行分析评价,根据回馈的讯息及时发现系统性问题的存在,并适时的采取措施以消除其影响,使制程维持在仅受随机性问题影响的管控状态,以达到品质管制的目的
应用SPC进行制程管制前,应确认以下常见误区:
● 在生产因素(e.g. 人机料法环)未加控制、制程不稳定时就使用管制图
● 制程能力指标不足时(e.g. CP<1)使用管制图
● 误用规格界限作为管制界限
● 发生报警时未即时处理异常
● 处理异常仅针对当点,未从整体系统角度思考、未区分common cause与special cause
PPAP
PPAP是在APQP的第四阶段(产品和流程验证)时触发的,提交任何新零件以及批准对现有零件或制程的任何修改都需要PPAP。客户可以在产品使用期内的任何时间请求PPAP。因此供应商必须保持品质体系,以便随时开发和记录PPAP提交的所有要求。
PPAP要求一般会分为五个等级:
● Level 1: 只提供零件提交保证书(Part Submission Warrant、PSW)给客户。
● Level 2:提供零件提交保证书、产品样品,以及部份supporting data。
● Level 3:提供零件提交保证书、产品样品,以及完整的supporting data。
● Level 4:提供零件提交保证书以及客户定义的其他要求资料。
● Level 5: 供应商在制造场地需要有零件提交保证书、样品以及完整的supporting data,以便检核。
在维基百科有说明PPAP应检附的文件
整个IATF16949的系统难以在本文完整阐释,若有实务经验相信会更能理解,坊间有许多顾问公司开设IATF16949稽核员课程,有志往品保领域发展可以考虑参与,在面临客户或第三方稽核时会更有把握。
五大工具则各有其发展历史,如SPC、FMEA皆有相当严谨的使用规范,对专项工具有兴趣者也可参考AIAG&VDA的官方文件,对原理、使用时机皆有清楚介绍。